Use case
Depalletizing a large variety of steel rods
THH Drehteile GmbH aimed to fully automate a manual manufacturing process — without making modifications to the transport containers and the way they are delivered to the machine.
Customer requirements
Random location of the rods inside framed Euro pallets
Arbitrary number of variants of partly specular rods
Uncertain placement of the pallet for processed parts
Customer benefits
Automation of manual labor for which nobody could be hired
Significantly increased throughput compared to the manual process
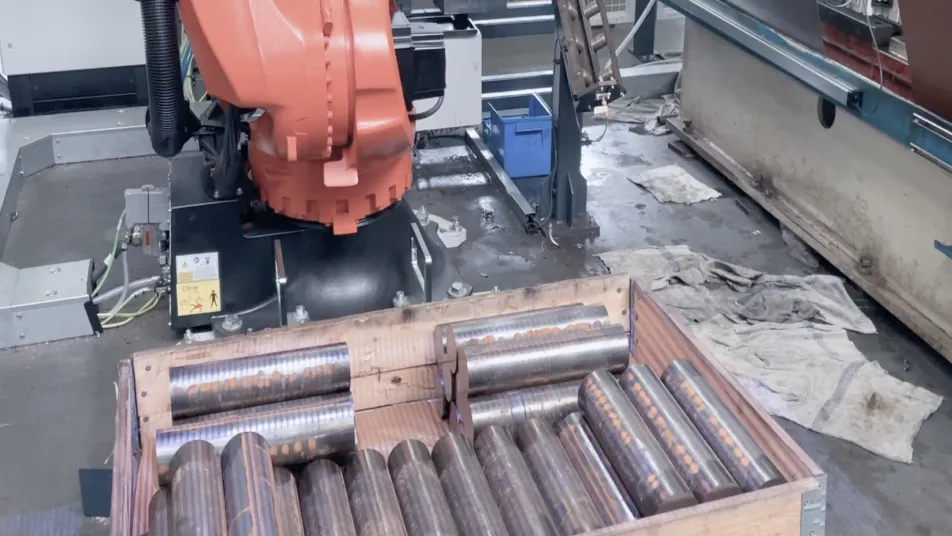
Components:
Robot
KUKA KR 120 R2700-2
GRIPPER
Goudsmit MS-8140405
HMS-PLAY50x2 MDC-50mm
Sensor
ZIVID 2
Vision SOFTWARE
Vathos Plane Picking
Edge Device
Sintrones ABOX-5000G1
PLC
Siemens SIMATIC
S7-1500 CPU
Integrator/Customer:
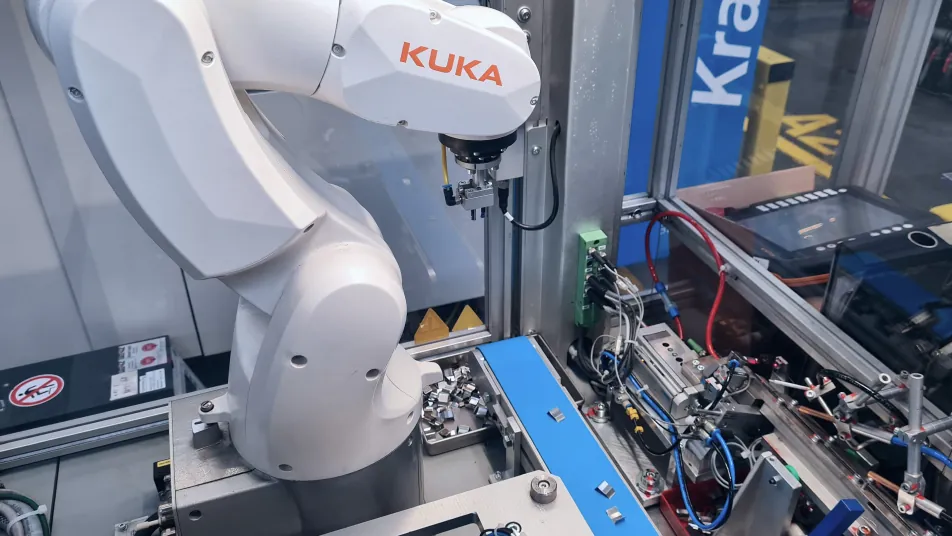
Components:
Robot
KUKA Agilus
GRIPPER
Pneumatic suction gripper
Sensor
BAUMER 2D VCXG-51M
Vision Software
Vathos Contour Picking
Edge Device
Advantech MIC-700
PLC
Siemens SIMATIC
Integrator/Customer:
undisclosed
Use case
Fast picking of specular parts from a conveyor
At a household appliances manufacturer, a feeder machine that was responsible for separating raw parts and bringing them into a well-defined position would clog and interrupt production at regular intervals. Vision-guided picking off a conveyor bypassed all problematic mechanical equipment and boosted the overall reliability of the system by a large margin.
Customer requirements
Highly specular 10x20mm metal objects
Approx. 2.5s per pick
Sub-millimeter accuarcy
Operational 24 hours a day, 5 days a week
Customer benefits
Reduction of inadvertent interruptions by 70-100%
Use case
Sorting and stacking of small load carriers
A variety of empty load carriers coming from an assembly plant need to be sorted and stacked, each type on a separate pallet. The goal of the project was to process a subset of the incoming load on a branch of the main conveyor with an industrial robot. Our solution provides the key capabilities of distinguishing different box types, locating, and placing them on precisely-interlocking layers.
Customer requirements
Distinguish >5 different types
Sufficient throughput
Reliable building of stacks
Customer benefits
Reduction of manual, monotonous work
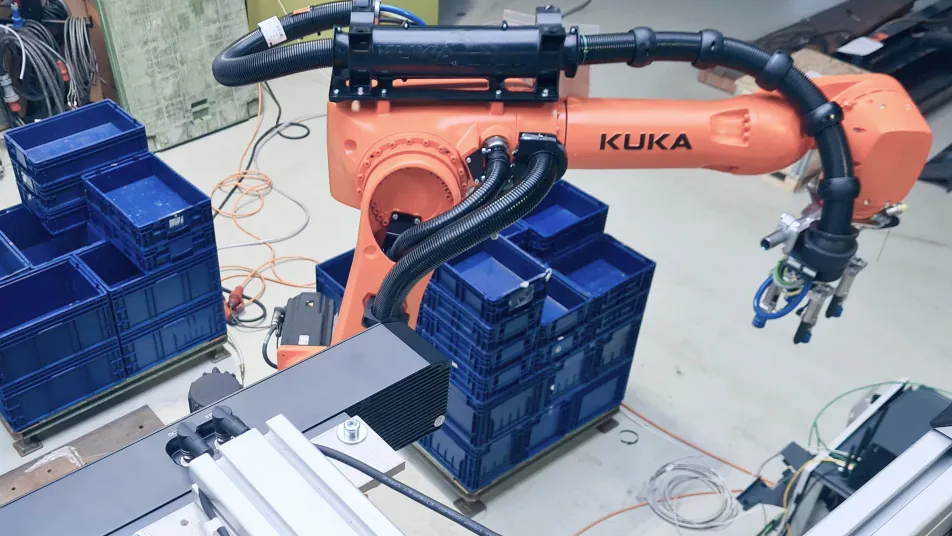
Components
Robot
KUKA KR 70 R2100
GRIPPER
Pneumatic suction gripper
Sensor
Zivid 2
Vision Software
Vathos Plane Picking
Edge Device
DELL Precision
PLC
Siemens SIMATIC
Integrator/Customer:

Components
Robot
Linear unit
GRIPPER
Component-specific
Sensor
BAUMER 2D VLG-12M
Vision Software
Vathos Inline Inspection
Edge Device
ADLINK
PLC
Siemens SIMATIC
Integrator/Customer:
Use case
Visual inspection of friction welding spots
The customer wished to monitor a series of three friction welding spots for completeness and any remaining small metal chips, that might scratch the surface in the following manufacturing steps. All images and the associated production parameters had to be stored for later analysis.
Customer requirements
24h operation, 5 days a week
Flexible integration into a special machine
100% remote maintenance and control
Customer benefits
Automatic, auditable quality control
Use case
Inline thermography of molded plastic parts
Incorrect temperature distributions on the tool are detrimental to quality in injection molding. We monitor the tool temperature indirectly by obtaining images of the part with an infrared camera instantly after ejection from the machine. Our software detects common error classes such as partial or complete failure of the cooling system, incomplete filling of the mold, or bead wire break.
Customer requirements
Integration into existing process
High variance of part types
Customer benefits
Holistic quality control
Independent of injection molding machine vendor
Inexpensive compared to cooling water measurement
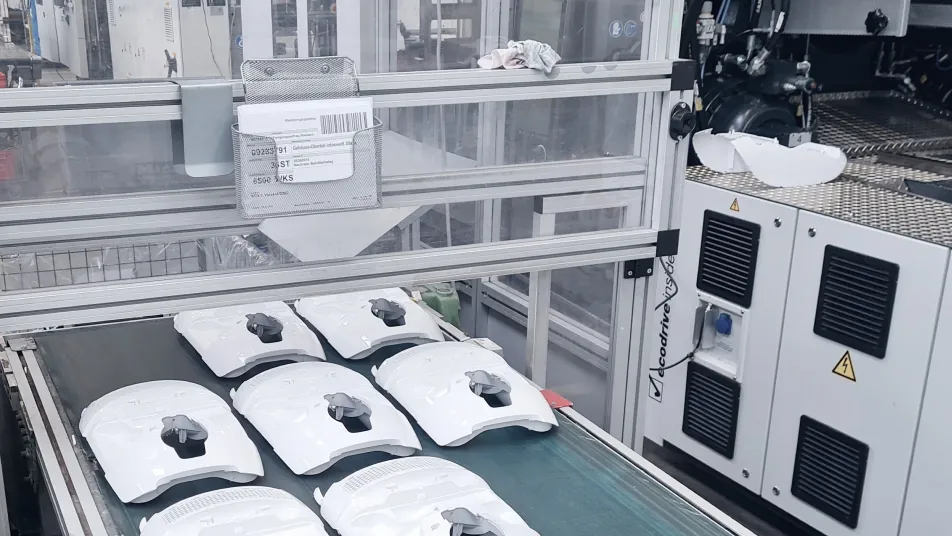