Holistic quality control
Inline thermography for quality assurance in injection molding
The quality of injection molding machine output depends crucially on the temperature distribution of the tool. Our inline thermography service detects critical deviations from a desired setpoint by continuous observation of the finished parts with an infrared camera.
# Fast alerts
# Easy to retrofit
# Simple operation

Why inline thermography?
Detection of errors early in the process
Today's quality control in injection molding still relies heavily on samples of the finished product. The problem is that (partial) cooling circuit failures and their impact on the material may go unnoticed for a long time, leading to a potential loss of an entire batch. By measuring quality close to the actual fabrication step, errors can be caught early on in the process. Inline thermography verifies the quality of each and every part leaving the machine — and is significantly cheaper and more reliable than competing solutions, e.g., based on measuring the cooling water temperature.
#
Inspection of every part produced
#
No more waste of entire batches
#
Useful for process optimization and control
Advantages
Seamless quality control at reasonable cost
Conventional methods for inline tool temperature monitoring, such as probing the cooling water circuits, are significantly more expensive (in installation and maintenance), as they require highly customized and complex mechnical modifications of the molding tool. Our inline thermography solution is 100% contactless and thus much cheaper while boasting all of the following advantages:
Inexpensive hardware
(less than EUR 1,500 with appropriate choice of edge device and camera)
Immediate alerts
(reports anomlies to the operator's mobile phone within minutes)
Auditable storage of all images
(in a central globally accessible location)
Easy to retrofit
(requires no modifications of tool and machine)
Supreme user-friendliness
(Only a few necessary parameters are controlled through a mobile app.)
Open data exchange interface
(for identifying root causes of errors by correlation of alerts and production parameters)
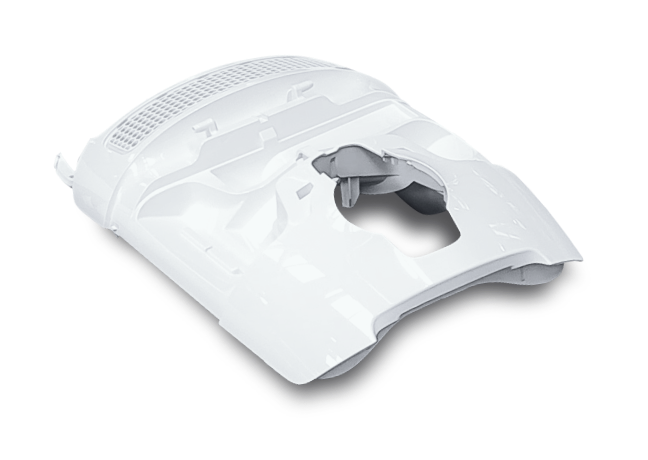
Typical molding errors:
Failure of cooling system
Incomplete filling
Bead wire break
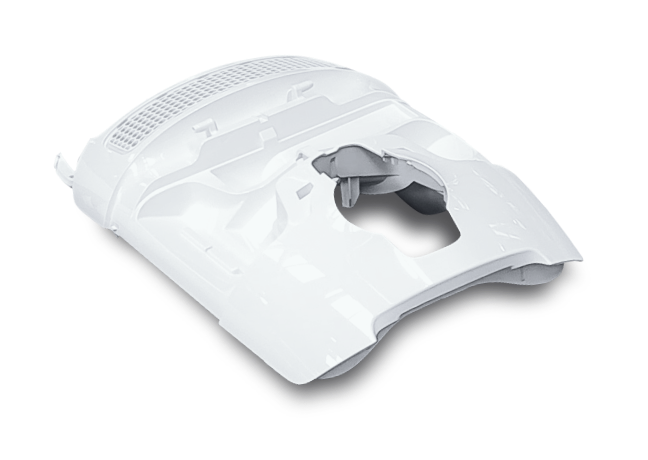
Error detection with infrared:
Breakdown in cooling system
Short shots
Missing components
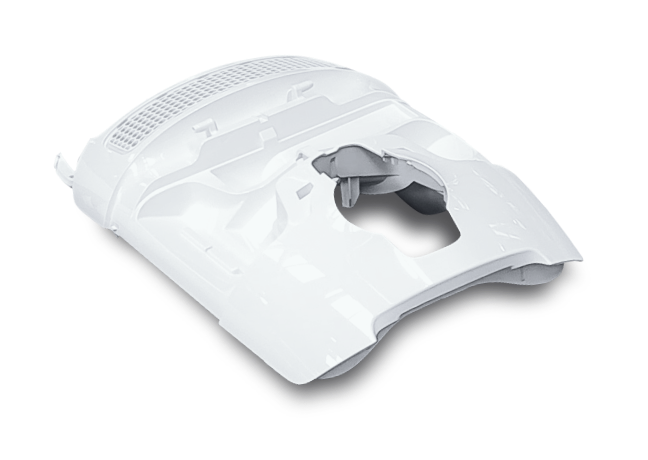
Error detection with infrared:
Breakdown in cooling system
Short shots
Missing components
Kostengünstige Hardware
(schon ab 1000 EUR pro Maschine durch variable Auswahl des Sensors)
Automatische Alarmierung
(z. B. per Email - System meldet Fehlerbild und Zusatzinformationen per Email auf das Handy des Werkers)
Revisionssichere Ablage der IR-Bilder
(meldet Temperaturabweichungen unmittelbar über Email/App-Benachrichtung und Bildschirm an)
Zugang der aller Produktionsparameter und IR-Bilder
(meldet Temperaturabweichungen unmittelbar über Email/App-Benachrichtung und Bildschirm an)
Herstellerübergreifendes, leicht nachrüstbares System
(da jede Lineareinheit das Bauteil nach Entnahme vor den Sensor halten kann)
Einfach verständliche Bedienung
(über Webbrowser mit wenig Eingabeparametern)
Monitoring at scale
Serving injection molding machine clusters
By combining an easy-to-use user interface with hardware tailored precisely to the inspection task at hand, even a large number of machines can be monitored inexpensively.
Hardware
Customers are free to select a sensor for optimal cost-value ratio: Simply monitoring the state of the cooling system can often be achieved by a cheap off-the-shelf IR camera. Larger parts or the desire to detect even small-scale defects may require the use of more expensive high-resolution IR cameras. Our solution allows for switching between a variety of imaging devices with the click of a button.
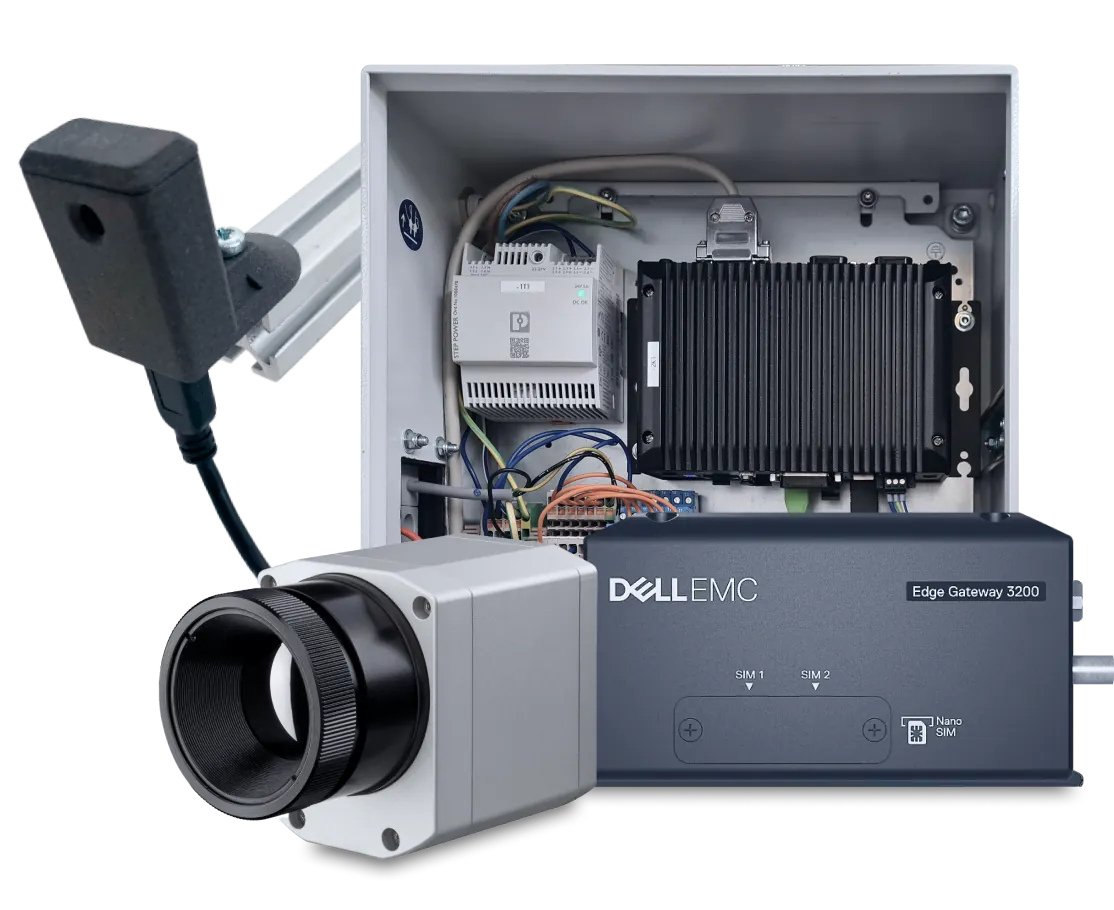
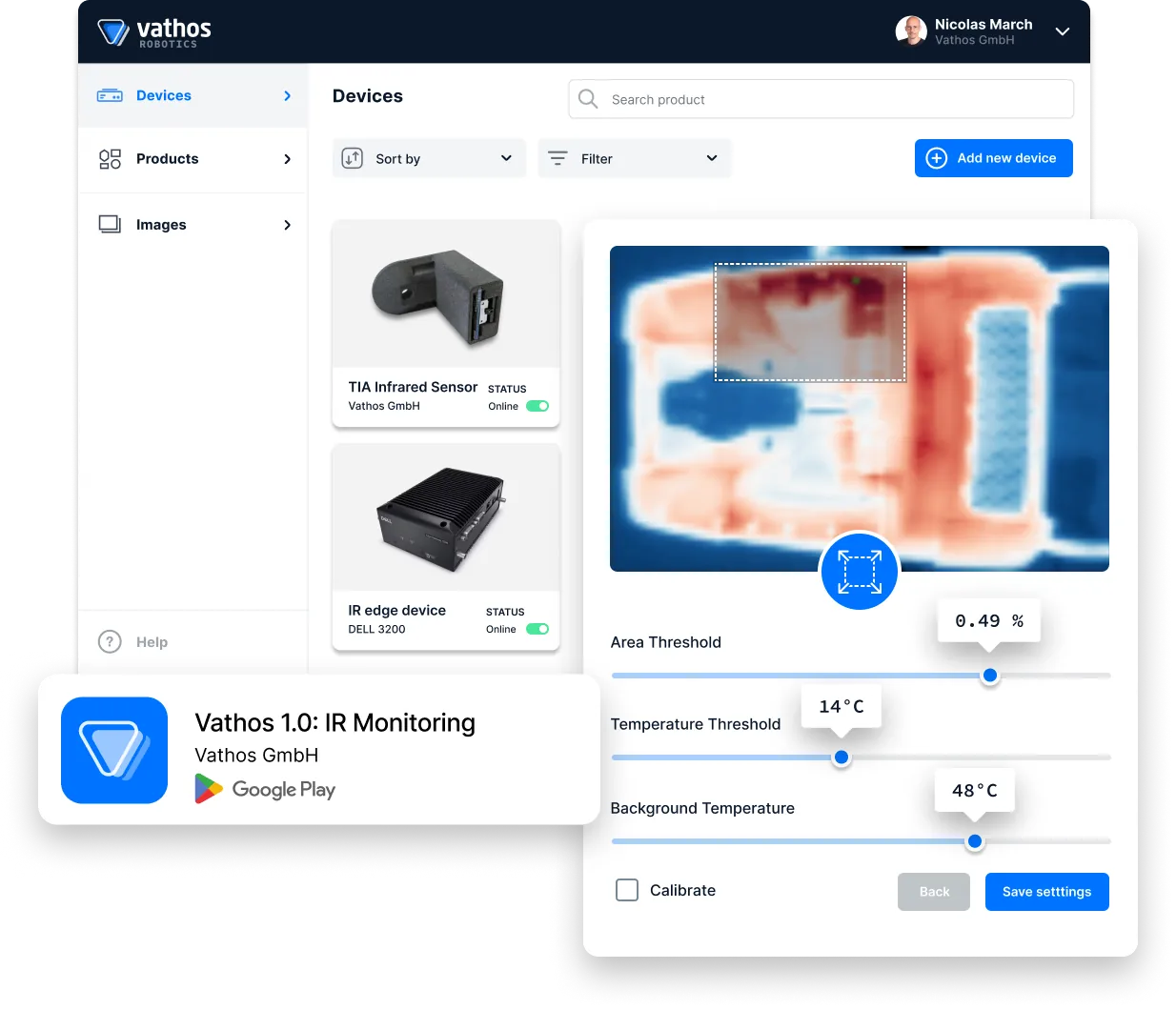
Software
In collaboration with seasoned injection-molding experts, we have optimized the user experience for those controlling monitoring parameters and reacting to alerts in everyday operation on the shop floor. Our mobile app is designed for maximal ease of use and presents all information gathered about error states in a way that is easily and unambiguously interpreted.